Risk Management

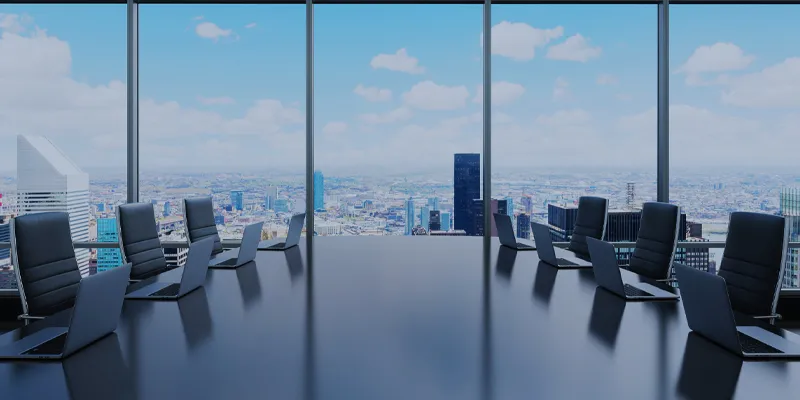
Risk Management System of Toyo Seikan Group
We have been performing risk management based on the “Rules for Group Risk and Crisis Management.”
The Group Risk and Compliance Committee and other relevant parties check the status of the group-wide risk management and take improvement and preventive measures.
Each group company has its own framework to promote risk management, under which it formulates the basic policy and plan of its risk management and conducts a review of its company-wide risk management status.
Risk and Compliance Framework
- This chart is scrolled
Significant risks
The following are major risks that may have a material impact on the Toyo Seikan Group's financial condition, business performance, and cash flows. In addition, Toyo Seikan Group's businesses and operations are also subject to various other risks.
- Natural disaster, infectious disease and accident risks
Business continuity and recovery from natural disasters / Infectious and communicable diseases / Occupational accidents and health and safety - Compliance risk
Compliance / Human rights violations and discrimination - Business management risk
Fluctuations in economic conditions / Fluctuations in production costs / Procurement of raw materials / Intensifying price competition / Research and development (R&D) / Investment and lending (Corporate acquisitions / capital participation / capital investment /etc.) / Digitalization / Customer credit concerns / Recruitment and development of talent / Litigation / Overseas operations - Information security risk
Leakage of personal information / Leakage of trade secrets and other confidential information / Cyberattacks and hacking by viruses - Financial and accounting risk
Financing / Changes in accounting standards and tax systems - Manufacturing and quality risk
- Environmental risk
- Country risk
For more details on significant risks, please refer to Annual Securities Report for Fiscal 2023 (PDF pages 39 and onwards).
Enhancing Risk and Crisis Management Framework
To address risks and crises that may affect the Group and to prevent risks that could disrupt our ongoing business, we have established the Risk Management Committee as an organization to strengthen group’s risk and crisis management structure. We have also established the Group Risk and Compliance Committee to oversee risk and crisis management and compliance across the Group. In addition, we have set up the Risk Management Administration Office as the secretariat for these committees. Both committees are responsible for verifying information related to significant risks and implementing improvement and preventive measures. Furthermore, in order to stabilize the management base, Toyo Seikan Group Holdings and its group companies individually develop crisis management rules and crisis response manuals and summarize their risk management situation under each management system.
Moreover, the companies reinforce their risk management systems based on their business continuity plans (BCPs), which have been formulated to quickly resume and maintain operations in the event of a crisis.
Addressing Infectious Diseases
On May 8, 2023, the Japanese government reclassified COVID-19 from Category 2 to less-severe Category 5 of the five levels of legally designated infectious diseases. As Toyo Seikan Group, we have complied with the government's policy and essentially lifted the basic measures for COVID-19 infection prevention. However, we continue to maintain a certain level of infection control measures, including prevention of the spread of other infectious diseases. In the event of an increase in infections or any other circumstances, we will work on strengthening our measures as necessary.
Activities Planned for FY2024
We will place high priority on the following five items in the Group’s risk and crisis management activities for the current year.
- Promotion of BCP activities across the group companies
- Confirmation of the status of risk management activities in each group company
- Reviewing and strengthening the training content in response to the increasing information security risks
- Formulate and disseminate our risk management policy
- Continued implementation of awareness activities for management regarding harassment
Organizations and Significant Risks of Operating Companies
Each operating company of the Group has established a risk management organization to prevent the occurrence of risks, and to resume normal operations as soon as possible if a risk event occurs.The risk management organizations identify significant risks that could obstruct business operations, and take responsibility for addressing such risks.
Company | Potential significant risk |
---|---|
Organization | |
Toyo Seikan |
Operation and management / Finance and accounting / Debt collection / Natural disaster and accident / Compliance / Information security / Manufacturing and quality / Environment / Country |
Risk & Compliance Committee | |
Toyo Kohan |
Compliance / Manufacturing / facilities / quality / Sales / Safety,hygiene,disaster prevention / Environment / Information Management / Human Resources |
Risk Management Committee | |
Tokan Kogyo |
Compliance / Manufacturing and quality / Environment / Finance and accounting / Information security / Natural disaster and accident / Country / Operation and management |
Risk & Compliance Committee | |
Nippon Closures |
Compliance / Natural disaster and accident / Debt collection / Information security / Quality / Environment / Country |
Risk & Compliance Committee | |
Toyo Glass |
Compliance / Natural disaster and accident / Environment / Quality / Information security / Debt collection / Country / Food safety |
Risk & Compliance Promotion Committee | |
Mebius Packaging |
Operation and management / Finance and accounting / Debt collection / Natural disaster and accident / Compliance / Information security / Manufacturing and quality / Environment / Country |
Risk & Compliance Committee |
Risk Management Activities of Group Companies
Activities for FY2023
BCP training implementation
Toyo Seikan
We conducted a company-wide BCP training exercise that assumed a scenario of multiple factories being simultaneously affected by a magnitude 9.0 Nankai Trough earthquake occurring during a holiday night. All business locations and departments, guided by instructions from the headquarters set up online, confirmed the reporting of damage situations and decision-making processes towards recovery based on the established BCP. We also utilized the disaster prevention portal site "BCPortal" for centralized management of necessary information, enabling reporting and confirmation of damage situations.
Toyo Kohan
Once a year, we conducted a joint BCP training exercise involving the head office and the Shimotsu business location. Through the training, we confirmed our communication structure and improved any deficiencies or issues related to scenarios of natural disasters.
Nippon Closures
We conduct twice-yearly response training exercises for the establishment of a disaster response headquarters and the utilization of our safety confirmation system.
Mebius Packaging
We conducted a BCP training exercise assuming scenarios of Mt. Fuji eruption and damage caused by linear precipitation zones. Each business location prepared scenarios related to natural disasters and confirmed their response procedures, making necessary improvements as appropriate.
TOMATEC
We conducted earthquake and tsunami evacuation drills. Additionally, we are a member of the Osaka and area stranded commuters council around the Umeda Station and participate in their training exercises.
Conducting a lecture on 'Autonomous Management of Chemical Substances'
At TOMATEC, we have been gradually implementing "Autonomous Management of Chemical Substances" based on the amendments to the Industrial Safety and Health Act Order, Industrial Safety and Health Regulations, and Specific Chemical Substances Hazard Prevention Regulations that were enforced on February 24, 2022. In order to promote and expand awareness of this initiative, we have been undertaking various efforts. As part of these efforts, TOMATEC Kyushu Plant organized an online lecture by a commissioned occupational physician. This lecture was attended not only by the Kyushu Plant but also by the secretariat of the safety and health committee in other plants, allowing us to deepen our understanding of the autonomous management of chemical substances based on legal requirements, including the importance of risk assessment, clarification of management systems, understanding and dissemination of the hazardous nature of chemical substances, and measures to reduce exposure.
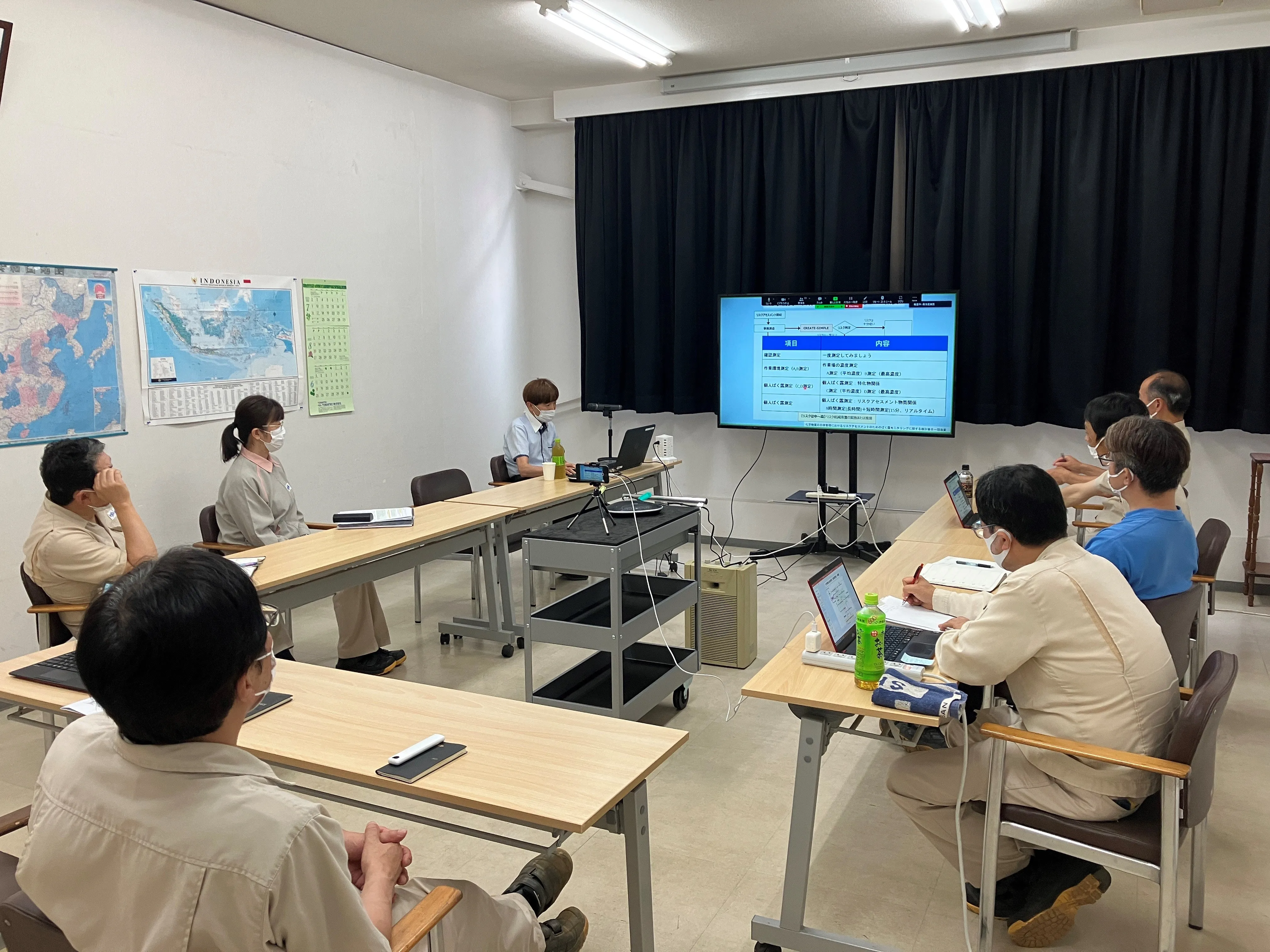
Activities for FY2022
BCP Drill at Toyo Kohan
Toyo Kohan has established rules for risk and crisis management, and regularly conducts drills to test its business continuity plan (BCP). After a three year hiatus due to the COVID-19 pandemic, the company resumed the training in fiscal 2022. The drill simulated a scenario where a fire at the plant would force a suspension of production for 45 days.
The head office and Kudamatsu Plant worked together to verify the procedures for an emergency, using a web conference system to share information on damage to equipment and product inventories and delivery schedules for customers. Following the drill, they identified issues to address and reviewed the existing rules and manuals for deficiencies. We will continue with the training to enhance its capability of emergency response.
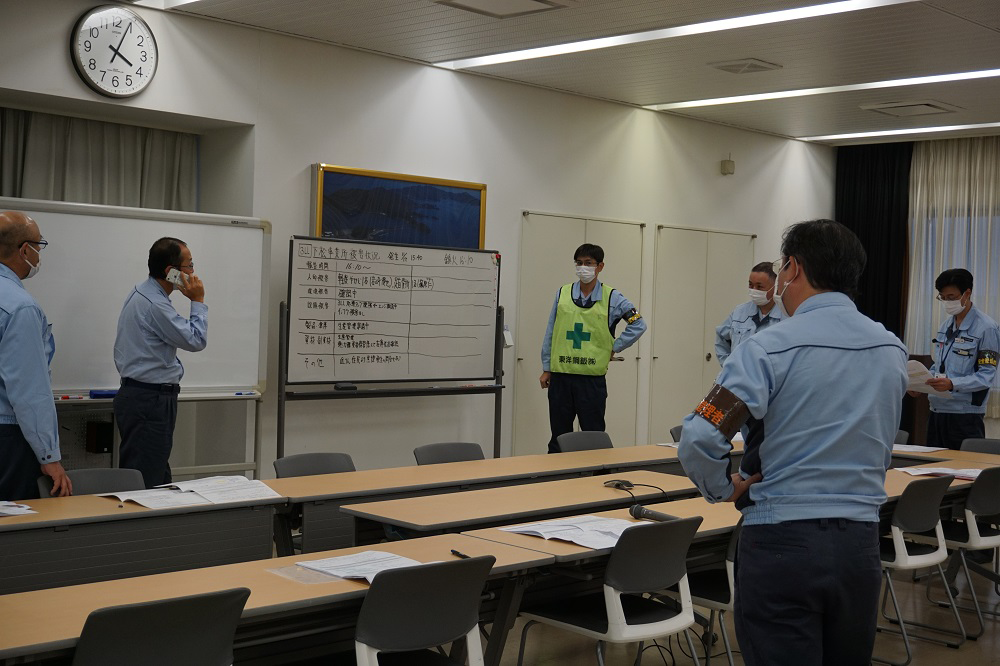
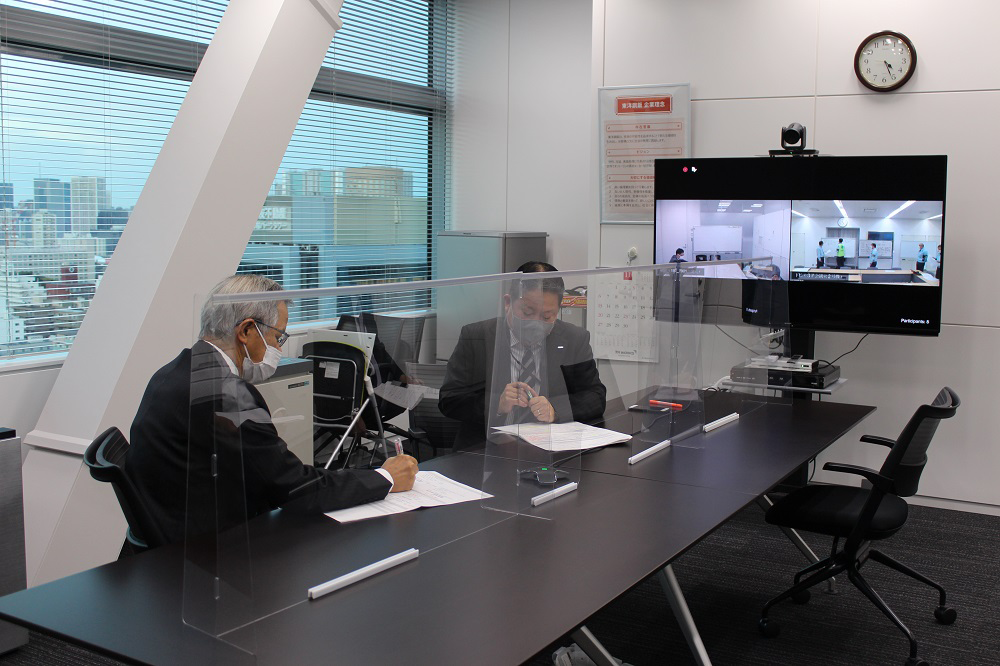
Formulating BCP and Conducting Drill to Prepare for Nankai Trough earthquake
Toyo Seikan has developed a BCP in anticipation of a potential megathrust earthquake in the Nankai Trough, which could cause simultaneous damage to multiple company plants. The BCP is designed to identify and prioritize tasks that would need to be addressed first in the event of such a disaster, thereby reducing the time required for recovery and ensuring the continuation of operations.
In March 2023, the company conducted a companywide drill based on the scenario of a Nankai Trough earthquake to test the effectiveness of its BCP. The drill involved setting up a virtual emergency headquarters,which communicated with all offices and plants via a web conference system and an online chat tool. Following instructions from the headquarters, each office and plant reported on their initial responses and the extent of damage to their facilities immediately after the simulated earthquake.
Training on Quality Emergency Response
At the Group, we have established guidelines to ensure a swift and organized response to quality-related emergencies, such as the distribution of products with significant defects or violations of quality compliance. To test the effectiveness of these guidelines, we conducted a simulated training exercise in collaboration with Toyo Seikan Group Holdings and selected operating companies.
The training was attended by relevant officers and department heads from both companies. They focused on checking the communication system during the initial response, the matters to be investigated, and the responsible departments, reviewing the entire processfrom the activation of the crisis response to the decision to disclose the issue. Any areas identified for improvement during the training were incorporated into the guidelines and shared across the Group.
Implementation of Information Security Education
As part of our risk management, The Group has beenimplementing education on information security sincefiscal 2022.
To protect the group companies from increasing cyberattacks, each member must raise their awareness of information security. We have provided all employees who have an email address with basic e-learning courses for information security management and simulation training for targeted e-mail attacks. With these programs,we are aiming to improve information security literacy in the workplace, such as increasing awareness in daily operations, to be more protected against cyberattacks.
In October 2022, during our month-long compliance promotion campaign, we invited a lecturer from TIS Inc., an IT service provider, to hold a training seminar for top management on information security compliance. The lecturer discussed the theme by referring to examples of compliance issues that actually happened, which helped the participants deepen their understanding.
We will continue to promote the importance of information security and carry out ongoing education.
Workshops on the Hazards of Chemical Substance at TOMATEC
At TOMATEC, we conducted workshops titled "Hazards of Chemical Substances Handled at TOMATEC", connecting the head office, Osaka plant, and other operational bases online. Additionally, under the auspices of the Health and Safety Committee at the company’s Kyushu Plant, we held workshops on the raw materials used in the pigment products, which were attended by many participants, including those in charge of manufacturing. In June 2022, during its “Hazardous Materials Safety Week”, we carried out internal patrols with a focus on verifying the management status of hazardous and toxic substances.
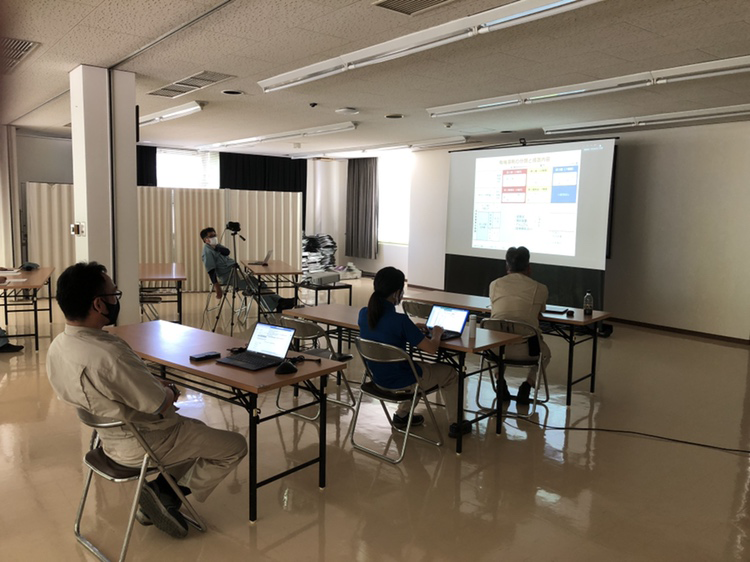