Quality Assurance

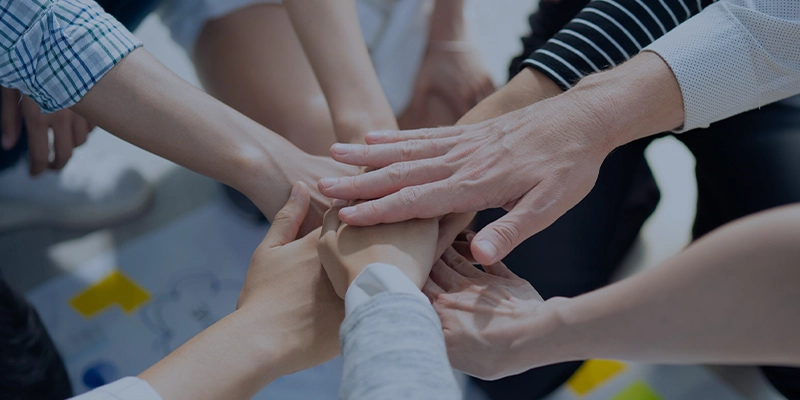
Quality Assurance Policy
Our quality assurance policy focuses on i) providing customers and society with products, systems and services that are safe and reliable and ii) implementing appropriate practices as a corporate group that deserves the trust of customers and society. Based on this policy, we are engaged in quality enhancement activities to maximize the value of all stakeholders.
Quality Management Organizations at Operating Companies
Our operating companies have established their own quality management organizations to improve the level of quality control.
- The table can be scrolled left or right.
Company name | Organization |
---|---|
Toyo Seikan | Central Integrated Management System Committee |
Toyo Kohan | Quality Management Committee |
Tokan Kogyo | Central Quality Committee |
Nippon Closures | Quality Assurance Department |
Toyo Glass | Integrated Management System Committee |
Mebius Packaging | Central Integrated Management System Committee |
Enhancing Quality Assurance and Product Safety
Construction of Quality Management Systems
Operating companies of the Group have constructed quality management systems to maintain and continuously improve the quality of their products, systems and services in accordance with the ISO 9001 standards. Among them, companies manufacturing and sell food containers have also established food safety management systems based on the FSSC 22000 standards, in order to provide safer products and increase reliability in the food supply chain.
Toyo Seikan, Toyo Glass and Mebius Packaging, in particular, operate a Total Management System (TMS), which integrates three management systems for quality (ISO 9001), food safety (FSSC 22000) and environment (ISO 14001). The system integration allows the companies to reduce overlaps in operations and expand their focus from sub-optimization to total optimization. Using the dynamic system that links their management systems closely with actual business activities, they are committed to promoting manufacturing that earns the trust of customers.
- The figure can be scrolled left and right.
Quality Assurance Education
Operating companies of the Group provide their staff with quality assurance training programs according to the characteristics of their operations and products. They are also engaged in quality enhancement activities using quality control methods to maintain and improve quality awareness among staff members.
Addressing Common Quality Risks for Group Companies
We collaborate across our group companies to address various quality risks, including major product defects, quality fraud, intentional product contamination, legal and contractual violations, product guarantees during severe disasters, and crisis management for quality emergencies. The quality assurance officers and department heads from both the holding company and each business company convene in the Group Quality Meeting to align the group’s direction and activities.
We place particular emphasis on preventing quality fraud, which could significantly undermine the trust of stakeholders. In addition to fostering awareness in accordance with the Toyo Seikan Group Code of Conduct, we are also working to reduce the reliance on individuals in inspection and measurement tasks. Furthermore, we conduct group quality audits led by the quality administration department of Toyo Seikan Group Holdings to inspect the current status of each factory and prevent quality fraud.