DX examples

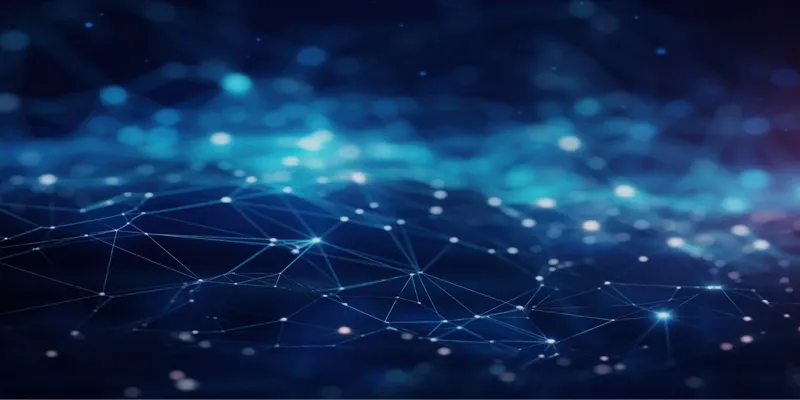
Three measures of focus
Transformation to a smart factory/office that realizes autonomous production and more efficient operating processes
To advance the digitalization and DX of the Toyo Seikan Group, it is necessary to collect and enrich information, integrate and accumulate it in an easily usable form, make correct decisions, and take actions based on analysis. By doing this, we are also taking account of the growing need to make proper decisions and take correct actions based on analysis. At production sites organized around missioncritical work, the Group is now taking steps forward in the visualization of data, its analysis, and its incorporation into measures. Also, in order to reflect this data analysis in parallel with monozukuri and business operations, we are enriching our internal educational offerings.
Promoting data collaboration throughout the supply chain
By sharing a diverse array of data across the entire supply chain, we can offer services not possible until today. To prepare for this, we are making the data accessible in real time, specifically information on product shipments and transport and environmental data such as GHG emissions reductions and preservation of water resources.
Application of IoT and DX technologies to expand business domains
Products and services derived from solutions to challenges faced by the Group could lead to resolving social issues. Because of this, we are undertaking development aimed at the expansion of business domains as well as their creation. Moreover, by leveraging digital technology so that we can make high-cycle iterations through marketing and R&D in new domains, our aim is to create value that builds on our strengths in such areas as materials development, molding, and engineering.
SaTeras IoT solution that advances digitalization at production sites to feed into improvements
We are developing our own SaTeras data collection package that achieves uniform management of manufacturing and production data. SaTeras offers the ability to have uniform collection and visualization of production data including specified conditions and measured values at manufacturing facilities, while also enabling analysis of the accumulated data in addition to advance detection of process faults and maintenance of high quality. The organization can now build a truly autonomous system.
We have completed the initial implementation at six aluminum can manufacturing facilities, both in Japan and overseas, and are proceeding with a series of trials at major group companies. SaTeras brings about new value creation by assembling the necessary features and services for a given installation. It does this by enabling flexible design of resource capacity expansion and through solving issues at manufacturing sites, including production efficiency improvements, while capturing our techniques and passing them on in software.
Offering users an environment allowing them to consolidate all data at a manufacturing site into a simple form
- Creating data consistency, maintenance-free design, retrofitting, and remote management
- Using data analysis to convert manufacturing know-how into digital form
- The table can be scrolled left or right.
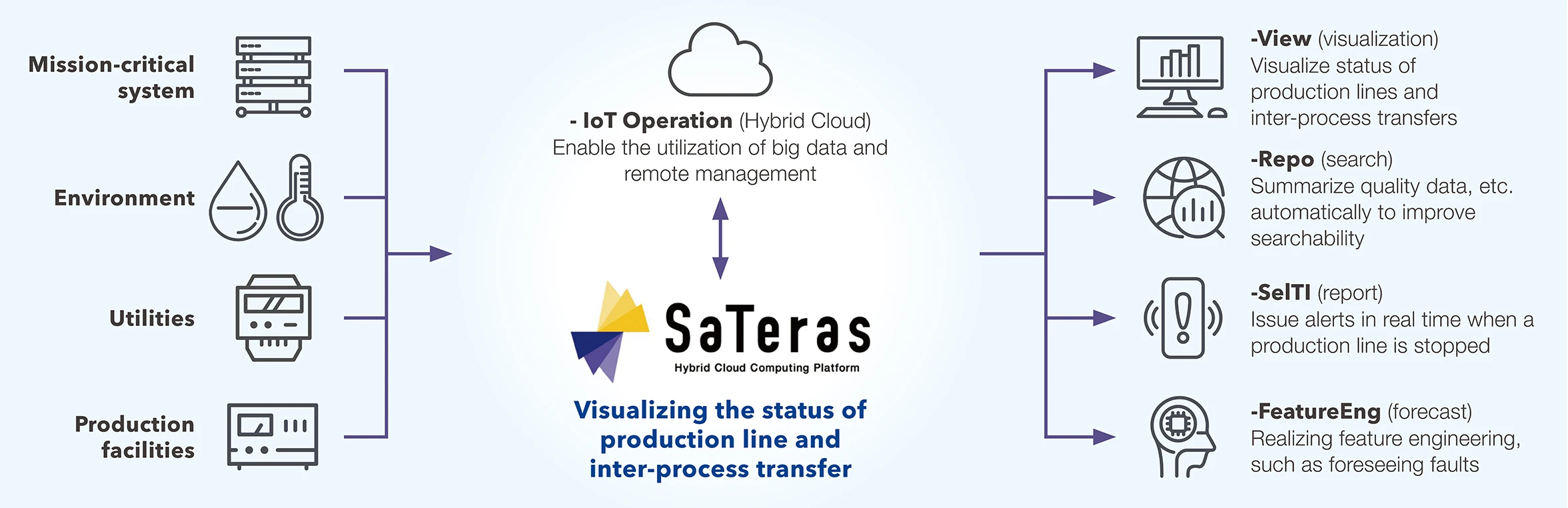
Fact, a core system for back-office efficiency that leads to optimized strategy
We have made major updates to Fact, an in-house core system, at the main group companies in the domestic packaging business. While integrating the basic modules, the design enables a flexible approach to customization at each company. We intend to use Fact to further the move to the paperless business, to make work more efficient through
automation, and to support work-from-home.
After completing the first implementations at the Toyo Seikan Co., Ltd. and Mebius Packaging Co., Ltd., we now plan a series of rollouts to major group companies in Japan. Hand in hand with this, we plan to add efficiency enhancements for deposits, withdrawals, and settlements
through subsystem development aimed at integration with management systems. We are also working on linkages with logistics and production management systems with the goal of optimizing sales strategy, roduction planning, and logistics procurement.
- The table can be scrolled left or right.
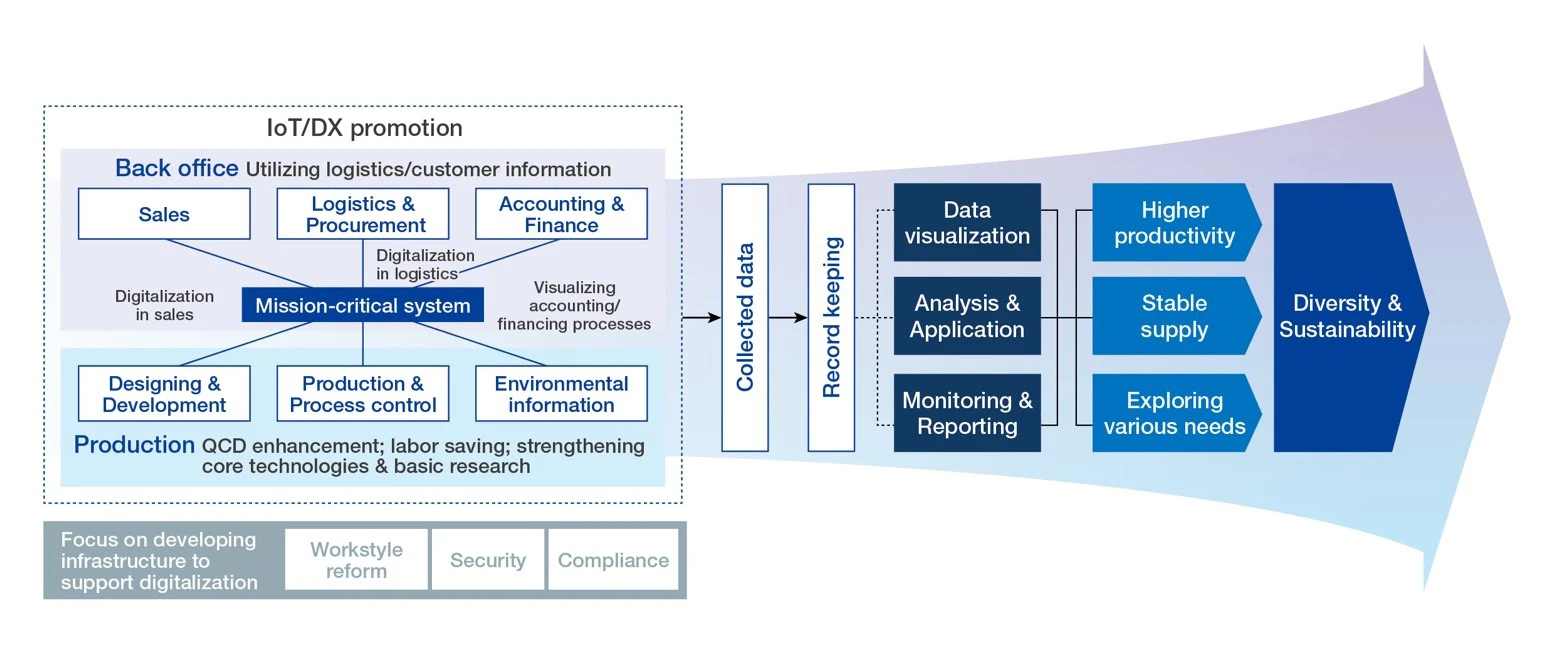
Outline of the use of digital technology in the Group
Toward Digital Human Resource Development
To raise the level of data use, it is vital to develop human talent that can make full use of data and digital technology, resolve management issues, expand business domains, and execute operations with greater efficiency. Specifically, the needs involve having the talent on hand to analyze data gathered from operational systems and facilities and then solve the problems in their own company and department as well as cultivating the human talent for employing RPA* tools for work automation to address the streamlining ofwork tasks.
And here, Toyo Seikan Group Holdings, which initiated DX literacy training for all Company employees starting in 2023, is out in front of the Group companies. Soon, it plans to roll out a similar set of initiatives to Group companies.
- Robotic Process Automation.
Human Resource Pyramid for realizing Group Digital Vision 2030
- The table can be scrolled left or right.
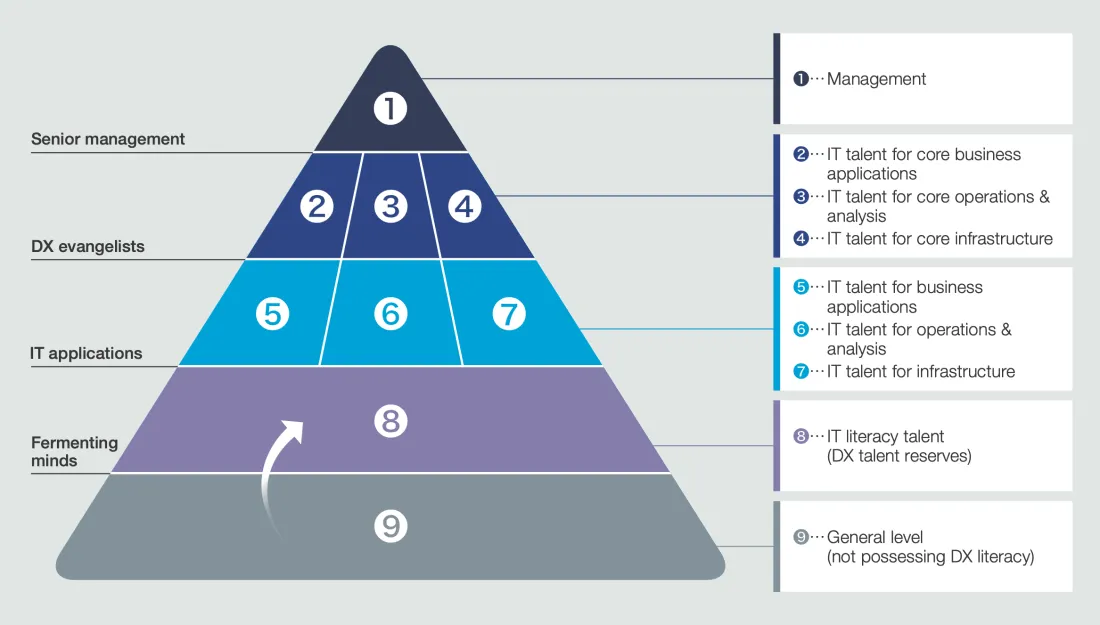
Status of RPA Applications
The Toyo Seikan Group is driving use of RPA applications for raising productivity and improving work processes. It seeks to have manual tasks automated on PCs so that employees can focus their efforts on higher-level work processes. For the six years from 2018 to 2023, inclusive, around 400 RPA work processes went live with a cumulative total of approximately 50,000 work hours saved. Up to now, the applicable domains have centered on mission-critical systems such as SCM and management systems such as human resources and accounting, and then spread to general affairs and purchasing. For the future, we are examining additional expansion to areas such as research departments.
Cumulative time saved through RPA
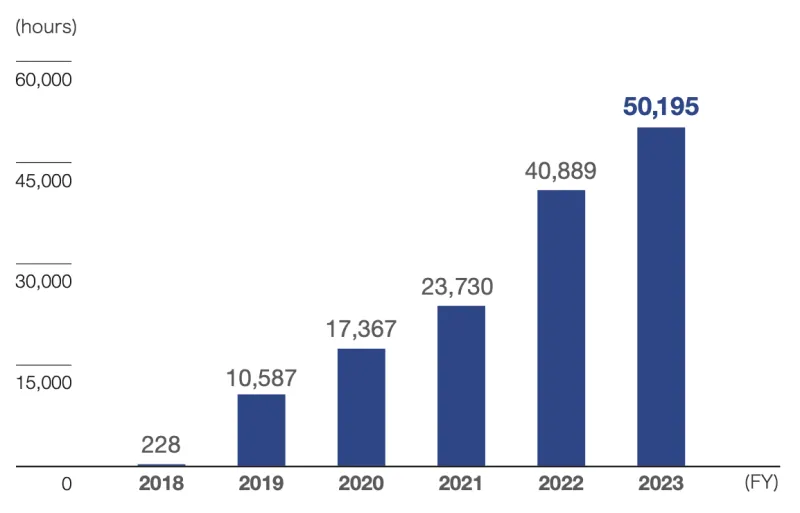