Respect for Employees:Health and Safety initiatives

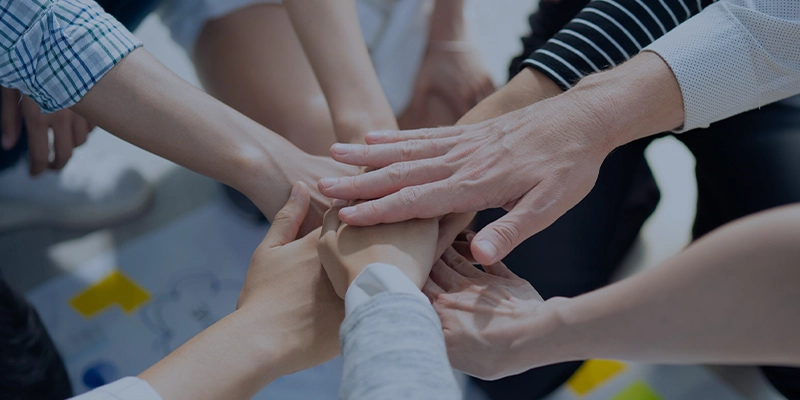
The Toyo Seikan Group is actively engaged in health and safety initiatives to ensure that all stakeholders can work in a safe and healthy environment. This includes not only our employees but also external stakeholders, partner companies, and contractors.
Our safety initiatives are centered on the committees of each company. These include workplace safety patrols, prevention of common accidents, and hazard prediction activities, all of which are carried out continuously based on the activity plan.
In our health initiatives, we are focusing on the prevention of lifestyle-related diseases and occupational diseases, and the promotion of mental health measures, in accordance with the annual activity plan.
Furthermore, together with our partner companies and contractors, we are implementing safety initiatives and disaster prevention events at our workplaces. Through these initiatives, we aim to create a workplace environment where everyone can work with peace of mind.
Our Approach to Occupational Health and Safety
The Toyo Seikan Group works to ensure comfortable workplace environment through the Toyo Seikan Group Code of Conduct, aiming and working toward creating a workplace where everyone can work with peace of mind.
Each business company, based on labor agreements concluded with labor unions and rules of employment, strives to ensure and improve the safety and health of its employees and takes the necessary measures to provide a safe and comfortable workplace.
Occupational Health and Safety Management Systems of Group Companies
At each of the domestic group companies, the president appoints the head of health and safety management (a director or an operating officer), who appoints the chief managers for health and safety of individual business facilities. Each chief manager establishes a health and safety committee to build a system to manage health and safety in the facility.
The health and safety committees established at each base operate as organizations promoting safety and health management, and they hold health and safety committee meetings with labor and management once a month.
The committee is composed of the chief manager, safety managers, health managers, an industrial physician, and other members representing the company and the labor union in accordance with laws and regulations. Half of the members are nominated based on recommendations from the labor union. If a major safety and health issue or concern is identified, it is promptly reported to the chief manager, instructions for correction or countermeasures are given by the Health and Safety Committee Secretariat, improvements are made in cooperation with the relevant department, and the content is horizontally deployed to other bases.
Preventing Occupational Accidents
To prevent occupational accidents, the heads of health and safety management of the group companies individually formulate their annual plans to carry out the activities stated below.
As part of our safety activities, we hold a Health and Safety Committee meeting at each base every month, where we strive to reduce risks by implementing continuous and proactive activities, such as formulating policies suitable for the characteristics of the workplace, safety patrols, measures to prevent the recurrence of common disasters, and KY (hazard prediction) activities. In addition, we share information on safety, such as examples of industrial accidents and measures to prevent them, with our partner companies and promote safety activities in collaboration with them. As for our health activities, we are working on the prevention of lifestyle-related and occupational diseases and the promotion of mental health measures.
We also have procedures in place for hearing from employees about near-miss incidents, information about potential problems, and proposals for improvement.
Frequency of Occupational Accidents
Number of Occupational Accidents, Number of Injuries, Number of Casualties
Item | FY2021 | FY2022 | FY2023 |
---|---|---|---|
Number of occupational accidents | 78 | 69 | 46 |
Number of injuries due to occupational accidents | 78 | 54 | 41 |
Number of casualties among the injured | 0 | 0 | 0 |
- Scope of aggregation: Toyo Seikan Group Holdings / Toyo Seikan / Toyo Kohan / Tokan Kogyo / Nippon Closures / Mebius Packaging / TOYO GLASS / Toyo Aerosol Industry / TOMATEC
Frequency rate, Severity rate
- The table can be scrolled left or right.
Item | Scope of survey | FY2021 | FY2022 | FY2023 |
---|---|---|---|---|
Frequency rate*1 | Toyo Seikan Group Holdings and its domestic consolidated subsidiaries | 1.29 | 1.72 | 1.09 |
All industries surveyed*4 | 2.09 | 2.06 | 2.14 | |
All manufacturing industry*4 | 1.31 | 1.25 | 1.29 | |
Severity rate*2 | Toyo Seikan Group Holdings and its domestic consolidated subsidiaries | 0.03 | 0.02 | 0.05 |
All industries surveyed*4 | 0.09 | 0.09 | 0.09 | |
All manufacturing industry*4 | 0.06 | 0.08 | 0.08 | |
Coverage of data collection among all employees of the Group*3 | 71% | 69% | 69% |
- Frequency rate: The number of fatalities and injuries caused by occupational accidents resulting in at least one day of absence from work or the loss of a body part or function / Total hours worked × 1,000,000
- Severity rate: Total workdays lost / Total hours worked x 1,000
- The coverage ratio is based on the numbers of employees as of April 1 of each year.
- Source: The Ministry of Health, Labour and Welfare’s Survey on Industrial Accidents
Activities of Group Companies
Activities for FY2023
Mebius Packaging Co., Ltd. Kawasaki Plant Receives Two Awards for Safety and Health Initiatives
Mebius Packaging Co., Ltd. Kawasaki Plant was awarded the Kanagawa labor director prize at the Kanagawa labor bureau safety and health awards ceremony held on July 7, 2023. The Kanagawa labor director prize is given to businesses that demonstrate a high level of safety and health standards in the region and serve as a model for other workplaces in terms of their efforts for improvement.
Furthermore, at the 59th Kawasaki-City industrial accident prevention workshop held on November 14, 2023, the plant was recognized for its achievements in preventing labor accidents and received an award from the Mayor of Kawasaki City. Inspired by these awards, we will continue to strive for the promotion of safety and health awareness in the future.
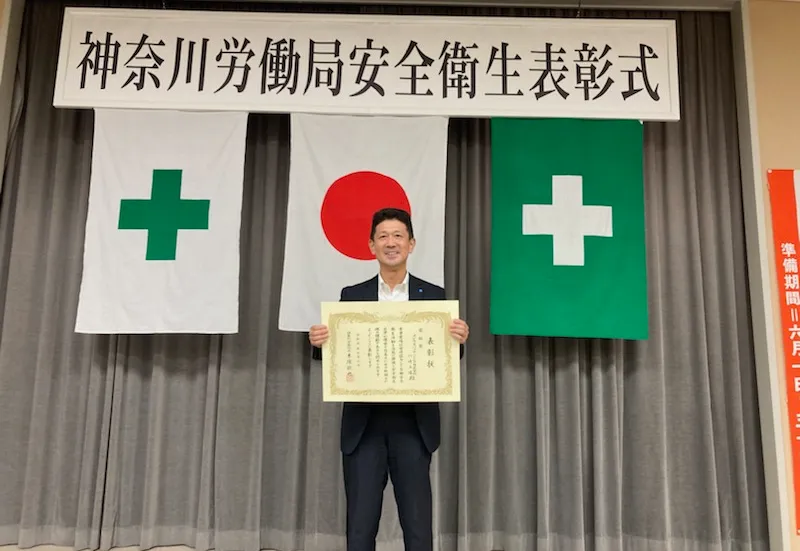
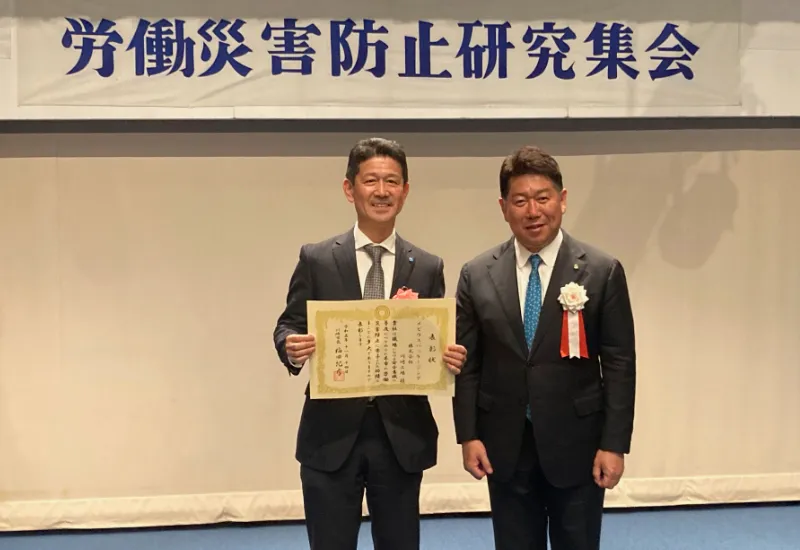
Utilization of "LaKeel Online Media Service" for Labor Safety and Health Education
Starting from April 2024, Mebius Packaging Co., Ltd. has begun utilizing "LaKeel Online Media Service" provided by LaKeel, Inc. as an educational tool for labor safety and health for all employees. Through e-learning, employees can efficiently learn at their own convenience, and by incorporating animated videos, they can gain a deeper understanding of the mechanisms behind labor accidents. Moving forward, by utilizing this service, which plays a part in Mebius Packaging Co., Ltd.'s labor safety and health education, we will continue to work towards creating a safer and more secure workplace environment, improving employees' knowledge, and preventing labor accidents.
Implementation of Safety Seminar
On June 19, 2023, TOYO GLASS CO., LTD. Chiba Factory conducted a safety and health seminar. We invited Mr. Takayuki Hasegawa from Create Co., Ltd. as the lecturer, and the seminar titled "Improving Awareness: Strengthening the Power of Observation" mainly targeted young employees who have been with the company for less than 5 years.
During the lecture, various topics were discussed, such as "Why is unconscious risky behavior worse than conscious dangerous behavior?" and "The dulling of the power of observation is more likely to occur when the desired state is not understood, is ambiguous, or is incorrect." Through group discussions, Mr. Hasegawa emphasized the importance of the power of observation and provided insights on how to enhance it. We aim to utilize the power of observation to identify and address potential risks in our daily operations, while maintaining a high level of safety awareness, with the ultimate goal of becoming a zero-accident factory.

Conducted a Seminar on Chemical Substances
TOMATEC organized a seminar on the management and regulations of chemical substances with the theme "Toxic and Hazardous Substances Handled at TOMATEC" on June 29th, 2023. The seminar was held online, connecting employees from various locations, and more than 80 participants attended. As TOMATEC handles a wide range of chemical substances, each with different hazardous properties and regulations to comply with, this seminar provided a valuable opportunity to deepen understanding among our employees. Furthermore, during the "Hazardous Materials Safety Week" in June 2023, we also conducted safety patrols with a focus on confirming the management status of hazardous materials and toxic substances.
Conducted Electrical Safety Education
In line with the Electrical Usage Safety Month in August 2023, TOMATEC invited an external lecturer to conduct electrical safety education. Over 40 participants from the head office, Osaka plant, and other facilities attended the training. The lecturer discussed examples of potential dangers such as tracking fires and the hazards of wire rolling on the floor, helping to raise awareness among the participants. The knowledge gained from the training was also applied during safety patrols to further enhance safety consciousness.
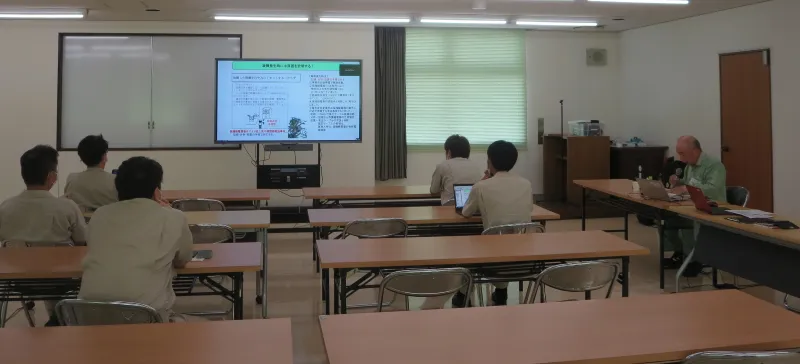
Conducted Safety Awareness Education Using Virtual Reality (VR)
At TOMATEC Komaki Plant, we implemented safety awareness education utilizing virtual reality (VR) in November 2023. With this education, participants were able to experience simulated labor accidents through virtual reality, enhancing their sensitivity to potential hazards. By immersing themselves in more realistic accidents and disasters, they were able to engage in reflective learning. This education was not limited to manufacturing personnel but extended to a wide range of employees, representing a new initiative that contributes to active safety and health activities. Representatives from Osaka and Kyushu offices also participated on the day, conducting mutual patrols. Participants exchanged opinions and ideas, leading to an improvement in safety consciousness.
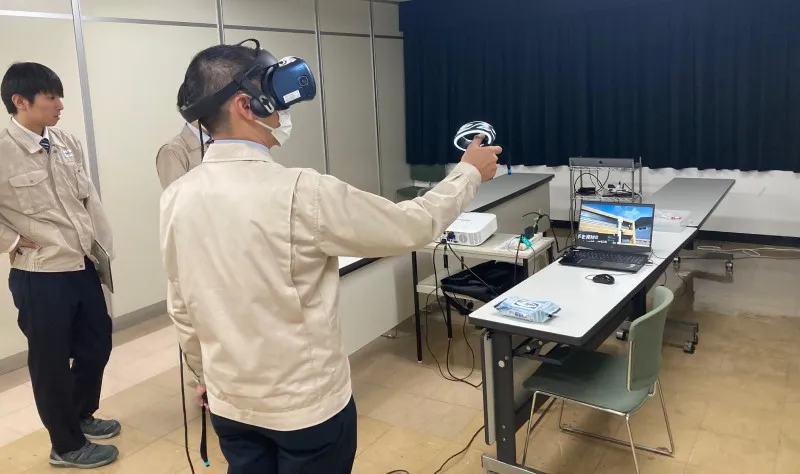
Implementation of Pre-Work Safety Measures
At Stolle Machinery do Brasil Industria e Comercio Equipamentos Ltda. in Brazil, we conduct Daily Safety Dialogues (DDS) activities before starting work each day to share information about safety measures. These dialogues involve lectures on the correct use of Personal Protective Equipment, proper lifting techniques for objects, and prevention of illnesses. Through these activities, we strive to enhance safety awareness.
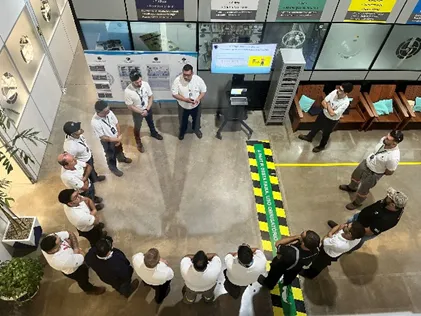